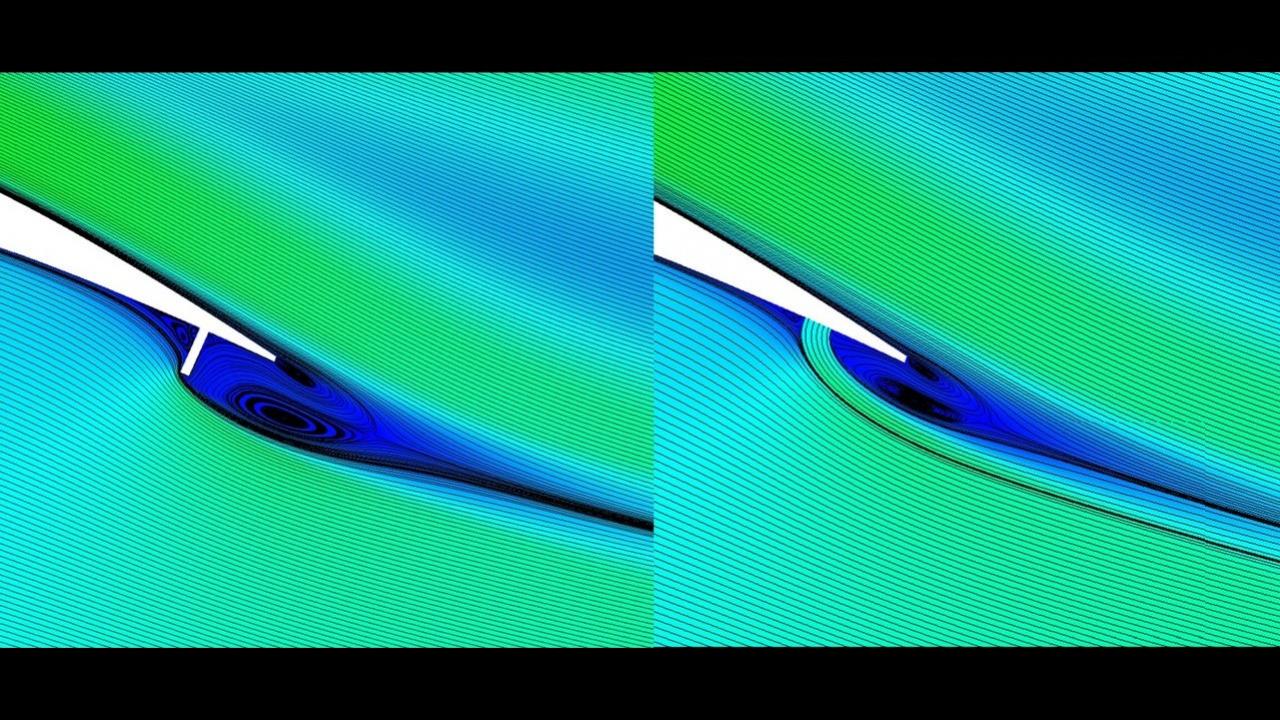
Putting air in airfoils
Mechanical and aerospace engineering professor Case van Dam and his team are developing new ways to generate lift in aircraft using microjets to blow air out at the trailing edge of an airfoil. With new funding from NASA Ames and interest from Boeing, the team, including recent Ph.D. graduate Seyedeh Sheida Hosseini, will prototype and refine their design and conduct wind tunnel tests at Texas A&M university to bring their technology closer to use in the field.
Generating lift is crucial for any aircraft, and the more lift a craft can produce, the faster it can take off and land. Changing airfoils, the cross-section of a wing or rotor that interacts with the air, is the simplest way to do this.
“With some small changes of the shape at the trailing edge of an airfoil, you can have a large effect on the lift,” said van Dam.
Changing the lift is important for taking off and landing very quickly in all types of aircraft. Shorter takeoffs and landings will make flight more accessible and open the door to short-distance air taxis and delivery craft—something both Boeing and NASA are interested in.
Through work funded by both NASA and Boeing, van Dam’s team found that blowing a small amount of air out of the airfoil’s trailing edge could have a significant impact on lift while being more efficient than traditional designs such as flaps and elevators.
“Instead of using these mechanical systems, which are clunky and heavy and sometimes cannot be deployed quickly, this gives you a way to quickly change the lift of a wing,” he explained. “It also gives you an additional control over the aerodynamics of a wing of an airplane”
With the new NASA funding, the team will produce 3x7 foot prototypes for large wind tunnel testing at the Oran W. Nicks Low Speed Wind Tunnel at Texas A&M University. With wind tunnel tests, they will be able to refine their design to figure out how best to blow the air out of the trailing edge and produce more lift while reducing drag.
Additionally, the team has been working with Boeing to address practical concerns about implementation in the field. Van Dam feels that thinking about these issues now will give them a leg up as they move the technology toward adoption. If the wind tunnel tests are successful, NASA plans to implement the design on their Common Research Model (CRM) airplane configuration for more advanced testing and further development.
Regardless of the eventual result, van Dam is proud of the progress the team has made and hopes it will make an impact both on the industry and on the students who have a chance to participate.