Francis Assadian partners with Ford to research innovative advanced controls and control system architectures
Professor Francis Assadian is working on two projects with Ford Motor Company to bring intelligent control systems design and artificial intelligence to enhance vehicle safety and performance and automating manufacturing.
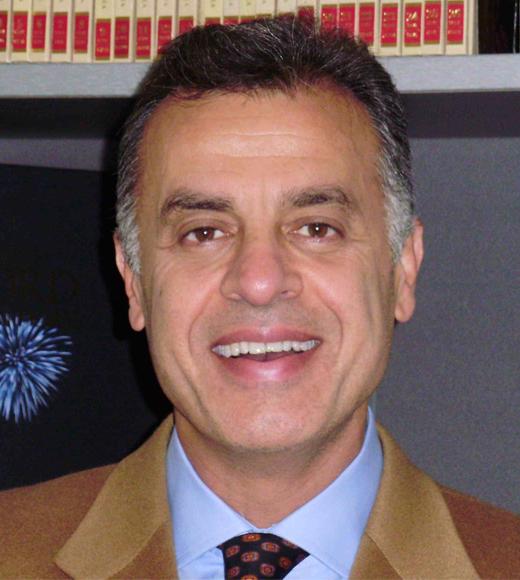
“We are working on new control development in both automotive and smart manufacturing, which is extremely important to the future of MAE,” he said. “All these activities we do in control systems, design and artificial intelligence is to make things at a lower cost without compromising performance, safety and quality.”
Toward a Universal Vehicle Control System
The first project, in collaboration with Ford Detroit, looks at vehicle control systems. He specifically focuses on control systems functional architecture, a framework that coordinates all the moving parts of a car including steering, braking and the engine and makes them work in harmony. As new active systems improve, car companies are investing more and more into designing intelligent control systems for their vehicles, but this can be expensive because vehicle types vary.
“Ford spends a lot of money when they go from vehicle-to-vehicle in order to change things when they’re designing control systems,” said Assadian. “There’s a lot of things that need to be changed and adapted and this is costly.”
Assadian’s solution is to develop a control system design with a new functional architecture that will maintain or improve fuel efficiency and performance while being a sort of one-size-fits-all design for Ford’s vehicles.
Artificial Intelligence for Smart Manufacturing
Assadian’s other project, with Ford’s Bay Area branch, focuses on smart manufacturing—the incorporation of AI in the manufacturing process. Ford hopes to use humans in more specialized roles on the manufacturing line while transitioning the more menial tasks to AIs. One example is taking screws, putting them in holes and tightening them.
“It’s a simple task, but it becomes complicated to accomplish this with artificial intelligence,” he said.
The project design involves two robotic arms. One holds the tool—a screw in this case—and the other has a camera that looks at the screw and the hole it needs to go into. The two arms work together to figure out which way the screw is facing and where and how to place it in a hole.
This requires developing a neural network, a type of machine learning modeled after the human brain. The network trains the camera about screw orientation, how to locate the hole and to precisely place and then twist the screw inside.
“This is just the start,” said Assadian. “If we are able to do these things, it will be extremely important for Ford and for all the other major automotive companies.”
Visit Assadian’s profile to learn more.